Honeycomb Packing Paper: Manufacturing Process and Use as a Filler Material
Manufacturing Process of Honeycomb Packing Paper
- Raw Material Processing
The production of honeycomb packing paper begins with the selection of high-quality raw materials. Typically, recycled paper or natural kraft paper, known for its strength and durability, is used. The paper is chosen based on fiber density, weight, and processing capability. The raw material preparation process includes the following steps:
- Collection and Recycling – Collecting used paper and recycling it for reuse.
- Pulping and Whitening – The paper undergoes a pulping process and is cleaned of unwanted fibers.
- Creation of New Paper Rolls – After processing, the paper is compressed and rolled into large rolls ready for further processing.
- Selection of Raw Materials
Honeycomb packing paper is made from recycled or high-quality kraft paper, which contributes to its durability and eco-friendliness. The paper used in production comes in large rolls and is selected based on strength, flexibility, and weight appropriate for its intended purpose.
- Initial Cutting and Processing
In the first stage of production, the paper is cut into long strips according to the desired dimensions. The cutting must be precise to ensure the structural stability of the honeycomb paper in subsequent stages.
- Creation of the Honeycomb Structure
After cutting, the paper passes through a specialized system that creates a pattern of hexagonal cells, resembling a natural honeycomb. This is a critical stage in the process, as it provides the paper with its unique properties – flexibility, shock absorption capability, and high structural strength.
- Stretching the Paper and Layer Adhesion
In some cases, multiple layers of honeycomb paper are glued together to enhance structural strength. The adhesion is done using an eco-friendly adhesive that does not affect the paper’s biodegradable properties. Stretching and adhesion contribute to forming a uniform layer of hexagonal structure, allowing diverse applications.
- Final Cutting and Packaging
After the unique structure is formed, honeycomb packing paper is cut into various sizes according to market demands. Finally, it is rolled or packed in sheets and sent to customers for use in packaging, shipping, and protecting fragile products.
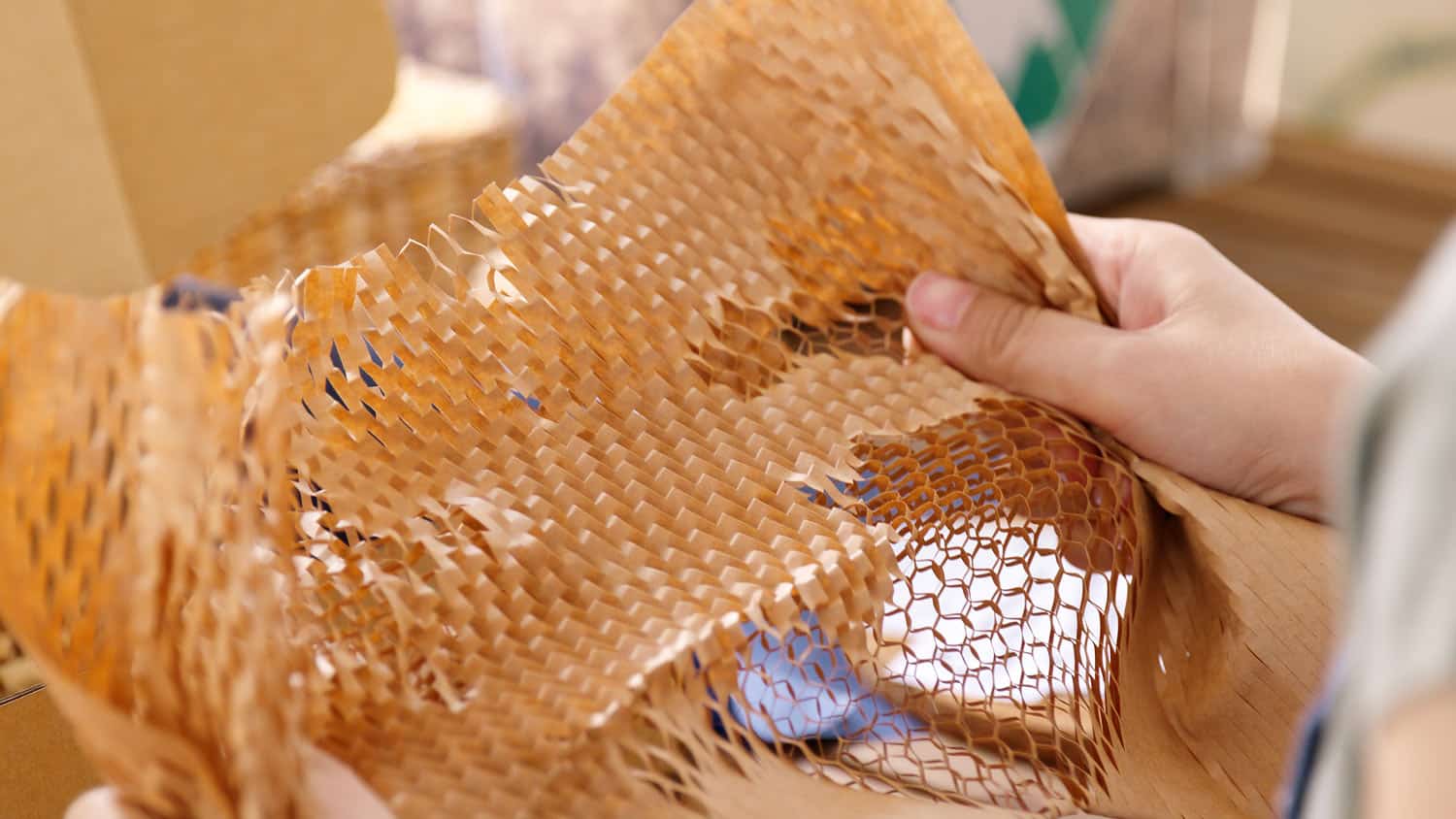
Essential Moving Tips
Honeycomb Packing Paper as a Filler Material
1. Benefits of Using Honeycomb Packing Paper as a Filler Material
Honeycomb packing paper offers an advanced packaging solution with many advantages:
Eco-Friendly – Made from recycled and fully biodegradable paper.
Lightweight – Does not add significant weight to shipments.
Flexibility and Customization – Can be cut and shaped as needed.
High Durability – The honeycomb structure provides excellent structural strength.
Shock Absorption Capability – Protects fragile products during transportation.
2. Primary Uses as a Filler Material
Honeycomb paper is widely used across industries, particularly in packaging, shipping, and storage:
Protection of Electronic Products – Provides excellent cushioning to prevent breakage.
Packing of Glass and Ceramic Products – Reduces damage during transport.
Filling Empty Spaces in Boxes – Prevents product movement within the packaging.
Furniture and Design Industry – Used as a base for lightweight but strong products.
Food Packaging – Utilized for eco-friendly and sustainable food packaging solutions.
Art and Craft Industry – A preferred material for eco-friendly artistic projects and creative designs.
3. Comparison with Bubble Wrap and Other Filler Materials
Honeycomb packing paper presents an excellent alternative to traditional filler materials like bubble wrap and Styrofoam. While bubble wrap is effective at shock absorption, it is non-biodegradable and environmentally harmful. Styrofoam, on the other hand, is lightweight but fragile, whereas honeycomb paper combines durability, eco-friendliness, and ease of use.
Feature | Honeycomb Paper | Bubble Wrap | Styrofoam |
---|---|---|---|
Eco-Friendly | ✅ Yes | ❌ No | ❌ No |
Lightweight | ✅ Yes | ✅ Yes | ✅ Yes |
Shock Absorption | ✅ Excellent | ✅ Excellent | ❌ Low |
Customizable | ✅ Yes | ❌ No | ❌ No |
Biodegradable | ✅ Yes | ❌ No | ❌ No |
4. The Future of Honeycomb Packing Paper
With the growing trend of sustainability and green packaging solutions, honeycomb paper is becoming a preferred choice for businesses and consumers looking to reduce their carbon footprint. Many manufacturers are investing in advanced technologies to optimize production and improve material durability, allowing it to replace polluting materials in a broader range of applications.
Moreover, innovations in honeycomb paper manufacturing are expected to lead to enhanced moisture resistance, greater flexibility, and even smart packaging solutions that can be integrated with digital tracking technologies.
5. Market Trends and Global Demand
The demand for eco-friendly packaging solutions is rising, and honeycomb paper is at the forefront of this shift. Studies show that the global market for biodegradable and sustainable packaging is expected to grow significantly in the coming years. Key drivers include:
Government regulations encouraging the reduction of plastic waste.
Consumer preference for environmentally friendly products.
Corporate sustainability goals aimed at reducing environmental impact.
6. Challenges and Opportunities in the Industry
Despite its advantages, honeycomb paper still faces challenges such as:
Production Costs – While manufacturing is becoming more efficient, costs remain higher than traditional plastic packaging.
Durability in Extreme Conditions – Exposure to moisture and heavy loads can sometimes affect performance.
Awareness and Adoption – Some businesses and consumers still rely on plastic packaging due to familiarity and availability.
However, as technology improves and awareness increases, honeycomb paper is expected to become more cost-effective and widely adopted across industries.
Conclusion
Honeycomb packing paper is an advanced packaging solution with numerous benefits, both in terms of its manufacturing process and its application as a filler material. Its unique structure provides strength, flexibility, and shock absorption, making it ideal for various industries, including logistics, electronics, and furniture. As a biodegradable and eco-friendly material, it stands out as one of the leading solutions in the future of sustainable packaging.